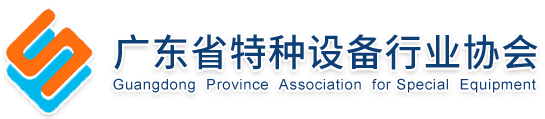
































扫二维码分享本页
前言
近年来,发生在起重机械操作过程中的惨痛事故也为数不少。殷鉴不远,如若我们不以此为戒,只会让血的教训再次在我们身上重演。看着那些因酿成事故而造成残缺不全的家庭,再看那些因失去亲人而悲痛欲绝的妻儿老小,我们的心不能不为之震撼!从他人的不幸中吸取教训,从思想上重视安全,从行动上落实安全,严格遵守各项操作规程,千方百计消除事故隐患,让安全成为习惯,是对自己、对家人最好的爱和最大的担当!
我们整理了近年来发生的起重机械典型事故案例,希望大家以典型事故案例为警戒,举一反三,加强教育和宣传,防范类似事故发生。
起重机典型事故案例视频
案例1:非法设备安全装置缺失 搬运工踏空坠亡
一、事故简介
2016年1月3日上午10时左右,某实业公司使用的一台简易升降机从4楼坠落到3楼,造成1人踏空跌落受重伤,经抢救无效死亡的事故。
二、事故原因分析
(一)现场调查
1.事故设备整体情况
事故设备是以一台电动葫芦为驱动装置,通过钢丝绳带动货厢,在井道内沿垂直方向运行的简易升降机。货厢内未设置内呼选层按钮,层站外有4组选层按钮(控制货厢的运行),1至4楼层门均设置有门锁,未设置有防断绳、防坠落、层门联锁、超载保护等安全装置。整台设备无出厂铭牌,未标注额定载重量、额定速度等参数,无检验合格标志,未办理使用登记手续。事故设备安装在某红木城楼梯转角处,现场勘查时,总电源已切断,货厢已降至1楼。
2.事故设备主要部件情况
(1)驱动装置情况
驱动装置是一台额定起重量2吨CD1型电动葫芦,上面有一块铭牌,标示内容为“起吊重量2t,额定电压380/220V,起升高度18M,起升速度8m/min,运行速度20m/min,制造日期2015年4月,上海轶鹰起重机械有限公司制造”。
(图1:事故起重机,电动葫芦铭牌,起吊重量为2吨)
(2)货箱情况
货厢为长方形,深度(纵向)为2.38米,宽度(横向)为0.84米,货厢出入口设置在横向(见图2),未设置货厢门。
(图2:货厢正面,货厢呈长方形,深度(纵向)与宽度(横向)比为2.83)
(3)导轨设置、导轨和导向设置配合情况
导轨设置于货厢纵向中部(见图3),货厢在导向装置约束下在1楼至4楼之间升降,导向装置与导轨之间存在一定的间隙(见图4)。
(图3:导轨设置)
(图4:导向装置与导轨配合情况)
3.事发过程调查分析
(1)该台简易升降机设计不合理,制造质量低劣,货厢深度(纵向)远大于宽度(横向),纵横比达到2.83,仅在纵向中部设置了导轨,且导向装置与导轨之间存在较大的间隙,配合不够顺畅。根据杠杆原理,当货物在货厢中不均匀分布时,极容易造成货厢失衡,在重力作用下货厢卡死在导轨上的现象。此时,如启动简易升降机下行按钮,电动葫芦放出钢丝绳,货厢由于卡死在导轨上,不能随着钢丝绳的伸长而下降,造成钢丝绳松弛不能再约束货厢。
(2)何某踏入货厢后,改变了货厢的平面受力状况,此时货厢重新获得平衡,卡死现象消失,由于未设置防断绳、防坠落装置,又失去钢丝绳的约束,货厢沿导轨急坠,直到钢丝绳约束住货厢,货厢才停止下坠。何某进入货厢后,罗某准备帮助何某搬运家俱,也往货厢走去,当他前脚踏入货厢的瞬间,货厢突然下坠,造成踏空,3层层门在事发时没有上锁,罗某跌进货厢后又被甩出货厢,跌到三楼楼层受重伤经抢救无效死亡。
(二)事故原因分析
1.直接原因
简易升降机发生故障后,搬运工罗某准备帮助何某搬出家俱进入货厢的瞬间,货厢突然下坠,造成踏空坠落受重伤经抢救无效死亡,是发生事故的直接原因。
2.间接原因
(1)事故单位安全主体责任不落实,安全生产管理不到位,在生产经营活动中使用非法制造、安装、未经监督检验合格和注册登记的简易升降机,当简易升降机出现故障后,只是口头提出要求,并未采取禁止进入货箱作业的有效措施,是发生事故的主要原因。
(2)何某和罗某安全意识淡薄,在进入已发生故障的简易升降机前,未采取防止简易升降机坠落的安全防护措施,是发生事故的次要原因。
三、事故防范和整改措施
(一)加大特种设备安全宣传教育。通过各种媒体和形式,宣传特种设备法律法规和安全技术规范,提高企业安全生产主体责任意识和安全生产管理水平,营造特种设备安全生产的良好氛围。
(二)开展简易升降机安全隐患排查整治工作。开展全市简易升降机专项整治,对整治中发现的非法制造、安装、使用的简易升降机一律进行拆除,消除安全隐患。整治中,如遇难以解决的重大问题,应及时报告当地政府协调解决。
(三)加强特种设备日常安全监督检查。强化特种设备安全监督检查,引导特种设备生产、使用单位严格遵守特种设备法律法规和安全技术规范,督促企业加强对特种设备从业人员进行安全教育和技能培训,建立并严格实施相关安全管理制度和安全操作规程,落实企业的安全主体责任;同时,特种设备安全监督管理部门要进一步加大“打非治违”力度,加强执法,严厉打击非法生产、制造、使用特种设备的违法违规行为,保持高压态势,确保特种设备安全运行。
案例2 无证人员违规操作 管桩坠落砸死货运司机
一、事故简介
2016年2月23日21时30分左右,某管桩公司无证吊车司机郭某和某物流有限公司拖挂车司机刘某在某管桩公司第三堆放场进行管桩卸吊作业,由于管桩两端不平衡,导致管桩脱钩,从拖挂车上坠落地面压到帮忙挂钩的司机刘某的头部,致刘某当场所死亡。
二、事故原因分析
(一)现场调查。发生事故的起重机属于双吊钩通用桥式起重机,双小车、双升降机构,在起重机2个吊钩上仍悬挂着索具,该索具为3组吊链及吊钩(自制专用吊钩)。起重机下方停靠1辆平板运输车(车头号牌为粤T14510、拖挂车号牌为粤T0974挂),车上存放有6根管桩(长约13m)。发生事故时所吊卸的管桩(长约13m,直径500mm,重量约为3t)已坠落在平板运输车右侧的行车道上,该管桩已有明显裂纹,平板运输车尾部右侧的行车道上有明显的血迹(为救出事故受害人已移动了坠落的管桩)。 事故设备为通用桥式起重机,出厂编号为S115118,规格型号为QE16(8+8)-25.5-A6,额定起重量为(8+8)t,起升高度为12m,起升速度为13.3m/min,大车运行速度为89 m/min,小车运行速度为43.8 m/min。事故起重机已办理了使用登记并在检验有效期内使用。
(二)事故原因分析
1.直接原因:
(1)管桩公司员工郭某(普工)无证上岗,擅自操作起重机进行管桩装卸作业,在操作中未能及时发现挂钩未到位的不正常状态且未等刘某走到安全区域便开始起吊管桩,导致在起吊过程索具脱钩、管桩坠落酿成事故。
(2)物流公司司机李某,违规擅自进行管桩挂钩作业,因未经过司索作业(挂钩)岗前培训、未掌握挂钩操作要领,操作不当(挂钩未到位)。
2.间接原因:物流公司刘某安全意识淡薄,自我保护意识不强,在起重机升降过程未按规定站在安全区域,管桩坠落时躲避不及被碾压致死。
三、事故警示
(一)事故单位应建立健全起重机械安全管理制度,制定并严格执行起重机操作规程。加强对起重机械作业现场的监督检查,杜绝无证上岗、违章操作等行为。
(二)事故单位应加强对起重机械相关作业人员的安全教育、安全培训和管理,尤其要重视新员工的安全教育和技能培训,要加强外协单位员工进厂安全培训工作。
(三)事故单位应加强对特种设备的经常性检查和经常性维护保养,及时消除安全隐患。
案例3 违规操作 保养工人遭小车挤压致死
一、事故发生的经过及救援情况
2016年2月24日下午15时30分左右,在某集装箱码头发生一起起重机械挤压事故,造成一人受伤经抢救无效死亡,直接经济损失146万元。
2016年2月24日下午13时30分左右,某机械公司何某(事故受害人)接到某码头公司工程部岸桥组对QC47#岸桥(事故设备)起升钢丝绳润滑的工作任务,随即安排机械公司员工蔡某与其本人共同执行,何某是该工作任务的项目负责人兼指挥手,蔡某负责执行具体润滑任务,码头公司安排其岸桥操作人员黄某协助配合。起升钢丝绳润滑作业依次分为机房卷筒、后大梁平台处、主梁与前大梁铰点附近、前大梁端部四个位置。当日15时30分左右,在完成铰点附近钢丝绳润滑工作后,何某、蔡某在小车顶收拾好工具物料,随后何某用对讲机指挥黄某将吊具拉到最高处后将小车从第三工位慢速向前移动至第四工位前大梁端部位置,此时蔡某蹲在小车顶右前区域,朝向前方靠海一侧,何某在蔡某左后边即小车顶左后区域,然后小车开始启动慢速往前移动。在小车还有几米到达大梁最前端时,蔡某听到何某“哎哟”声就立即用对讲机呼叫“停车”,小车马上停下,蔡某回头看到何某被夹在前大梁左侧减速传感器支架和小车左后侧液压缓冲器无杆腔及支座之间,当时何某意识清醒,叫蔡某和黄某帮助他侧身并扶起至小车顶中间位置,随即黄某通知岸桥组主任张某赶到现场,发现何某受伤情况后,紧急拨打120急救电话,大约16:00左右,120急救车到达现场,约16:30左右,120急救车将伤者送到人民医院,经医院抢救无效,于19:40左右宣布伤者死亡。(后经法医鉴定,死亡原因为失血性休克)
二、事故发生的原因和性质认定
(一)直接原因
事故发生后,某区市场监督管理局委托市特种设备安全检验研究院对事发起重机进行了技术勘验。根据该院出具的编号为2016AHJ40009的《特种设备事故技术分析报告》显示,事发起重机质量、安全性能满足相关要求,此次事故与设备相关结构及机构的安全性能无直接关联,这次事故的直接原因是起重机维保工(何某)违反操作规程,在岸桥小车开动过程中,没有退回司机室顶部安全位置,而是进入小车架顶部的作业禁入区域,以致被岸桥小车挤压导致其受伤死亡。
(二)间接原因
1.事故单位未履行应有的责任义务,对员工进行足够的技能和安全培训,作业维保人员的安全意识淡薄;
2.事故单位安全制度落实不到位,对日常起重机维保现场的巡查管控措施不力,对发现的违规作业现象未能及时制止;
3.事故现场维保作业人员何某不严格依规按章维保起重机械设备,个人作业行为随意,其应急反应和处置能力明显不足。
三、事故防范和整改措施
(一)事故发生后,区市场监督管理局立即组织辖区港口码头企业以及相关起重机械维保企业负责人事故安全警示会,通报事故情况,要求相关企业吸取事故教训,严防事故发生。
(二)区市场监督管理局立即组织对事故单位的许可资质及维保业务开展情况进行一次全面检查,责令其加强起重机维保业务和人员管理;同时进一步细化完善和落实公司内部相应安全管理制度,切实杜绝类似事故的再次发生。
(三)市市场监督管理局召开全市起重机械安全生产工作会议,通报事故情况并部署相关专项整治工作,要求起重机械相关企业开展隐患大排查,严查薄弱环节,严堵安全漏洞。要求各辖区局加强起重机械安全监管力度,重点查处起重机械未注册登记使用、超期未检、违规开展维护保养作业、作业人员无证上岗、安全管理制度不健全等违法行为。
(注:《深圳经济特区特种设备安全条例》第二十五条规定,电梯、起重机械的维护保养单位应当取得相应许可。)
案例4 无证司机野蛮操作 管桩坠落砸死路人
一、事故发生过程及伤亡情况
(一)事故发生过程
2016年5月2日22:05分,某建安公司起重机司机陆某(未取得起重机械司机证件)利用起重机将3根管桩吊运至货车上,在卸货完成后,陆某违规操作,在未能确定自制吊具完全起升到管桩最高处以上时,运行大车运行机构,引起自制吊具意外钩起1根管桩,产生斜拉后自制吊具从管桩内孔脱落,导致该管桩坠落,砸中从货车旁边经过的朱某。
事故发生后,建安公司立即向110、119报告及申请救援,某医院于2016年5月2日22:14分许到达现场,确认朱某已经死亡。
(二)事故伤亡情况
事故造成一人死亡,事故直接经济损失约110万元人民币。
二、事故原因分析
(一)直接原因
陆某违规操作导致管桩坠落,砸中朱某,致其死亡。
(二)间接原因
1.建安公司起重机械安全管理不到位;
2.陆某无证操作;
3.朱某违规进入作业区域。
(三)主要原因
1.陆某违规操作,无证操作;
2.建安公司起重机械安全管理不到位。
(四)次要原因
朱某违规进入作业区域。
三、预防措施和整改建议
(一)起重机械使用单位应加强特种设备安全管理工作,依法履行特种设备安全主体责任,聘请有相应证件的人员从事起重机械作业,加强对起重机械作业人员的安全教育及技能培训工作,建立健全起重机械安全管理制度,明确各自岗位职责,制定科学合理的安全操作规程,确保起重机械安全使用。
(二)充分发挥社会公众、从业人员和企业的监督作用,进一步加大对违法行为的打击力度,构建起重机械安全监管社会共治体系。
(三)进一步加大对特种设备安全的宣传力度,提高起重机械使用单位的特种设备安全意识和管理水平,推动企业落实安全主体责任,提高群众特种设备安全使用知识和安全防范意识。
图1起吊管桩用三肢吊索
图2 两套起升机构和双小车
图3 吊索起吊管桩图
案例5 野蛮操作,班长被钢梁挤压致死
一、事故简介
2017年12月5日,某桥梁钢构有限公司生产车间发生一起物体撞击、挤压事故,工人在利用二车间一台20t通用桥式起重机(以下简称起重机)把摆放在平板过跨车(以下简称板车)上的H型钢构件(以下简称构件)从一车间转运到二车间过程中,经桩柱C49与桩柱C50之间时构件发生摆动,对站立在构件与桩柱C49之间的一名人员李某造成物体撞击,既而挤压,致使其死亡。
事故现场照片
二、事故原因分析
(一)现场调查
1.相关人员
根据使用单位介绍,事故现场涉及3人。李某(死者,是该桥梁钢构有限公司某班组带班班长,该班组负责以钢结构制作分包的形式承揽桥梁钢构有限公司的部分钢构件生产加工任务),该次构件过跨作业的带班班长,负责协调指挥作业;起重机操作人段某远,负责起重机的操作,控制构件过跨及起吊作业;起重吊装辅助人员段某国,协助作业,辅助挂钩及钳挂吊钳。
2.起重设备及相关索具
发生事故起重机于2017年9月15日监检合格,检验报告和使用登记证齐全。在现场勘查后对起重机进行检查试验,遥控器外观完好,操作按钮复位良好,起重机功能正常,状态良好,主要零部件及安全部件未见缺陷,可排除设备故障引发事故。
起吊构件使用的索具为吊环上穿两条装有钢板吊钳的环链组成,整个索具未见缺陷,吊钳钳夹功能正常。
3.视频资料
车间中间的桩柱C50两侧分别装有监控摄像头,摄像头从北往南方向分别监控一车间和二车间。两摄像头可以观察到事故现场,根据摄像两个摄像头的视频可以大致观察和推断事故经过。
摄像头一(一车间,视频文件为ch01_20171205115400.mp4)
据视频可见,需过跨的构件放在板车约正中位置,从一车间往二车间移动一段距离后,此时构件还平放在板车上,未与板车分离。李某拿着钢卷尺从二车间往一车间走过来,然后把卷尺勾在构件靠一车间一端头,再从一车间往二车间行走测量构件,走到构件与桩柱C49之间时,构件被吊起并从北向南往桩柱C49摆去,把李某撞击挤压到桩柱C49、及桩柱上用扁钢板固定的气体管阀上。之后马上有两名人员过来查看情况,构件从南向北移开,李某被抬走。
摄像头二(二车间,视频文件为ch12_20171205115500.mp4)
据视频可见,起重机挂着松开的吊钳从二车间方向往一车间方向开到尽头,下钩,斜拉拖着地上物件往回走,李某过来查看地上及起重机小车状况。过一会儿,起重机挂着松开的吊钳再次从二车间方向往一车间方向开到尽头,此时李某手拿卷尺,勾住构件靠二车间一端头往一车间方向行走测量。两名操作人员站到构件上面,将吊钳分别钳挂在构件中间的两侧板,由于起重机钢丝绳未与地面垂直,起吊后的构件迅速摆动撞到桩柱C49。操作人员跳下构件,查看碰撞状况,操作起重机把构件往板车上吊运。
4.现场勘查
1)作业方式
经现场试验,空板车两人无法推动,放上构件后更加无法使用人力推动板车过跨。根据视频资料中起重机吊索具的运行轨迹,及对相关人员的询问可知,操作人员利用二车间的起重机先将吊钳夹住住一端,利用起重机小车斜拉牵引构件,构件并不与板车分离,利用斜拉构件产生的水平分力及构件与板车间的摩擦力,使构件连同板车一起从一车间过跨到二车间。
2)构件一侧搭放在板车上,另一侧悬空未见支撑,构件通过吊索具和吊钳被起重机悬空半吊着。北边吊钳钳夹在距离构件东端5.87m,南边吊钳钳夹在距离构件东端5.81m,即吊索具的吊点在构件中间偏东约0.13m,基本接近构件中点(见下图)。吊点离构件高度约9m。
2)构件尺寸为12×1.7×0.6m,由一块腹板两边各焊接一块侧板,组成H型的钢构件。腹板尺寸为12×1.63×0.025m,侧板尺寸为12×0.6×0.035m,整个构件重约7.8t。起重机吊点中心向南偏离板车中心即大致构件原中心1.04m。根据视频碰撞及碰撞后起重机钢丝绳位置状况,事发前起重机吊点应在桩柱C49附近,即吊点偏离构件斜拉水平距离约2.7m。构件一侧板有明显曾被吊钳钳夹的痕迹(见下图),据使用单位介绍,可能为此前加工及调运留下的痕迹。
3)过跨板车尺寸为8.07×2.5×0.76m,其行走轨道总长20m,即一车间、二车间各铺设10m,轨距1.5m,其轨道铺设在桩柱C49与C50的中间,桩柱C49与C50距离为5.5m。桩柱C49北侧用一1000×100×10mm钢板经拉爆螺栓安装固定了三根管阀在桩柱上,估算碰撞前管阀突出桩柱表面约0.17m。固定管阀的钢板弯曲变形,钢板两侧变形翘起,靠西侧的二氧化碳和压缩空气管阀有断裂、碰撞破损痕迹(见下图)。
5.过程分析
根据视频资料及对相关人员的询问,当时李某手拿卷尺从构件二车间一端往中间测量,到原已有的钳夹痕迹即大概构件中点位置,确定大概的起吊钳夹点,让两名操作人员先进行预钳夹,自己再走到一车间一端准备测量另一端的距离,以确保钳夹吊点为构件中点。在李某确定构件大概的钳夹位置后,操作人员下放起重机吊钩,两人攀爬并站在构件上,把吊钳分别钳夹住构件两侧板,并在未走下构件的情况下直接操作起重机起吊构件。在构件起升时,李某刚好在一车间构件的一端往二车间方向测量构件中心位置,走到构件与桩柱C49之间。由于吊点向桩柱C49方向偏离构件中心约2.7m,构件被斜拉吊起,根据构件的偏斜量及吊点高度之间的三角函数可计算出偏离角度约17度,同时根据构件的重量可计算出起吊时起重机对构件施加的水平分力约为23.4KN,再加上构件自身重力造成钟摆效应,致使构件迅速摆向桩柱C49,对李某产生物体打击,并把桩柱上的管阀撞断撞损,同时固定管阀的钢板也被撞击弯曲变形。由于构件吊点在二车间,构件撞击桩柱后发生了转动,但构件的宽度大于板车与桩柱的距离,构件没有完全脱离板车。事故发生后,操作人员稍微起升构件,把构件吊回板车,构件只是一边被吊回板车,另一边仍悬空吊挂。(示意图)
(二)事故原因分析
1.直接原因
起重机操作人员段某远严重违反安全作业规程,在未确认指挥信号、未确认起重机械吊具是否垂直、未对周边安全状况进行检查确认的情况下,违规站在要起吊的钢梁上直接操作起重机起吊钢梁,由于起重机斜拉起吊钢梁,使起吊的钢梁产生钟摆效应,在起升时发生了水平偏移并撞向李某所在一侧厂房的C49桩柱,将李某挤压在C49桩柱上导致事故发生。
2.间接原因
事故单位落实安全生产主体责任不到位,相关管理人员责任不落实,对质量体系文件和安全管理制度的执行力度不够,起重机械安全技术规范和作业指导书对起重作业没有起到指导作用,外包人员的安全教育和培训内容在起重作业中未得到落实,同时,对起重机械作业人员作业情况检查不认真不到位,未及时纠正违章作业行为,致使外包人员在起重机械起吊作业过程中未遵守安全技术规范和作业指导书要求,公司安全管理员也未及时制止违规作业,导致事故发生。
三、事故警示
(一)开展全员安全教育和特种设备安全技术规范及作业指导书培训不能流于形式,不能出现培训有记录,但现场操作作业时不按规章规定执行的情况。
(二)企业没有强有力的安全管理,就会出现质量体系文件和安全管理制度的执行力度不够,安全监督管理和制度不落实,保证安全生产的措施不到位的情况,难以及时消除安全隐患。
(三)由于外包作业人员存在流动性大、整体素质偏低,执行安全制度和操作规程时容易出现偏差,所以强化外包作业人员安全教育培训和外包作业现场安全监督,落实安全生产主体责任,是防范同类事故发生的重要措施。
案例6 违规操作 操作者被吊物挤压致死
一、事故发生过程及伤亡情况
(一)事故发生过程
2018年2月25日15时22分左右,某五金制品公司员工蒋某(死者)在模具组立车间内,独自操作一台电动葫芦桥式起重机(以下简称“涉事起重机”)进行合模。在合模过程中,涉事起重机起吊的模具(以下简称“涉事模具”)向蒋某方向快速移动,致使蒋某被挤压在起吊模具和另一台放在旁边的模具之间。该五金制品公司员工立即向110、120报告并进行了现场救援活动,但由于蒋某的头部和胸部受到严重挤压,2018年2月25日15时40分左右,120医生到场确认蒋某已经死亡。
(二)事故伤亡情况
事故造成一人死亡,事故直接经济损失约100万元人民币。
二、事故原因及性质
(一)直接原因
蒋某使用涉事起重机对涉事模具进行合模时操作不当,导致涉事模具快速移动并撞到旁边的模具,自身被挤压在这两个模具之间,致使事故发生。
(二)间接原因
涉事起重机遥控手柄按键操作指示标识脱落,相关标识无法辨认,易导致操作失误。蒋某在违规操作涉事起重机时,事故单位未能及时发现并对其违规行为进行制止。
(三)主要原因
1.蒋某违规操作;
2.事故单位起重机械安全管理不到位。
(四)次要原因
事故单位总经理刘某对该公司起重机械安全管理监督不到位。
三、预防措施和整改建议
(一)起重机械使用单位应加强特种设备安全管理工作,依法履行特种设备安全主体责任,加强对起重机械作业人员的安全教育及技能培训,建立健全起重机械安全管理制度,明确岗位职责,制定科学合理的安全操作规程,督促监督作业人员按章操作,确保起重机械使用安全。
(二)充分发挥社会公众、从业人员和企业的监督作用,进一步加大对起重机械违法行为的打击力度,构建起重机械安全监管社会共治体系。
(三)进一步加大起重机械安全宣传力度,提高起重机械使用单位的安全意识和管理水平,推动企业落实安全主体责任,提高起重机械从业人员技能水平和安全防范意识。
案例7 违规操作 操作者被吊物挤压致死
一、事故简介
2018年3月12日上午10时许,某水泥制品厂工棚内,一名起重机械操作工罗某在地面操作一台10t电动单梁起重机起吊一个组合模具,当被吊模具提升时,因模具重心与起重机起升中心偏离形成侧向斜拉,操作工罗某躲闪不及被挤压在两个模具之间,送医院后抢救无效死亡。
二、事故原因分析
(一)现场勘查
1.该水泥制品厂涵管模具为钢质,内径规格80-135cm,呈圆柱状壳体结构,由螺栓将两爿弧形钢模组合固定而成,其内腔为水泥涵管成型母模。
2.事故起重机械为电动单梁起重机,型号为LD10-15.82A3D,额定起重量为10t,起升高度为12m,事发时由操作工罗某在地面操控。
3. 事故发生时所吊模具内径为100cm,外径为120cm,总质量约3.8t,其中钢模质量约2t,水泥涵管约1.8t。
(二)事发过程调查分析
1.事发前,该水泥制品厂作业班组(共3人,含起重机操作工罗某)正在工作。员工A正在制备混凝土,为开机投料浇注模具作准备(与操作工罗某相距约5m,中间有物体阻隔视线)。员工B正在松卸其他待拆组合模具的部分螺栓(与操作工罗某相距约10m,中间有物体阻隔视线)。
2. 事发时,操作工罗某正准备将模具吊到拆卸台整体拆卸,当被吊模具被提升约70cm高度时,因模具重心与起重机起升中心偏离,形成侧向斜拉,此时操作工罗某正处在起重机主梁正下方被吊模具与另一个放置于地面的组合模具形成的缝隙间(缝隙宽约140cm),被吊模具离地后朝操作工罗某身体侧向移动约100cm,因无人照看指挥和提醒,操作工罗某躲闪不及被挤压在两个模具之间,胸腹部受到重创并引起颅脑损伤,送医院后抢救无效死亡。
(三)事发起重机情况
事发起重机类别为电动单梁起重机,型号为LD10-15.82A3D,额定起重量为10t,起升高度为12m,起升速度为7m/min,依法办理使用登记,在检验合格有效期内使用,事发由操作工罗某在地面操控。
(四)事故原因分析
1.直接原因
起重机操作人员罗某违章冒险作业,未严格按照操作规程,在没有指挥人员照看指挥的情况下独自操作起重机,起吊前没有前后左右观察重物是否与起吊中心重合,起吊时速度过快,被吊重物侧移对其挤压,导致其本人死亡。
2.间接原因
该水泥制品厂未认真落实安全主体责任,特种设备作业安全管理不到位。对一线作业员工的日常教育培训流于形式,日常安全生产检查走过场;未切实落实安全生产责任制和特种设备安全管理制度;未能及时制止和纠正员工长期存在的特种设备违章冒险作业行为;未按要求做好充分的安全生产准备工作即仓促实施节后复工。
三、事故警示
(一)起重机使用单位应加强起重机操作人员的安全意识教育和操作技能培训,使其掌握安全操作起重机的必备技能。
(二)起重机使用单位应落实特种设备作业人员的岗位责任制度,严格落实起重机械安全管理各项制度,健全安全技术档案,完善安全操作规程。
(三)起重机使用单位应加强对特种设备作业现场统一协调和管理,确保现场管理人员在职在岗,对无视安全生产的行为要坚决予以纠正和处理。
案例8 违规操作 同伴被轮胎挤压致死
一、事故发生过程及伤亡情况
(一)事故发生过程
2018年5月29日15:10左右,某货柜码头有限公司集装箱正面吊运起重机司机黄某和熊某在对一台集装箱正面吊运起重机(以下简称“涉事起重机”)进行打黄油保养时,熊某在未确认黄某具体位置的情况下,转动方向盘,导致黄某被涉事起重机的右后轮胎(以司机在驾驶位的方向为参照,下同)和平衡配重夹住并挤压。事发后,该公司开展了现场救援行动,同时该公司立即向110、120进行了报告及申请救援,医护人员在当天15:30左右到达了现场,黄某经抢救无效于当天17:20左右死亡。
(二)事故伤亡情况
事故造成一人死亡,事故直接经济损失约140万元人民币。
二、事故原因及性质
(一)直接原因
熊某与黄某在对涉事起重机进行维护保养过程中,熊某在未确认黄某离开润滑工作面的情况下,操作方向盘转动后轮,致使黄某被涉事起重机的右后轮与平衡配重夹住并挤压致死。
(二)间接原因
事故单位未制定集装箱正面吊运起重机润滑作业的具体操作规程,对作业人员专业技能培训不够,且黄某自身安全防护意识不足,在事发时进入了润滑工作面的危险区域。
(三)主要原因
1.事故单位起重机械安全管理不到位;
2.熊某操作不当;
3.黄某安全防护意识不足。
(四)次要原因
事故单位副总经理郭某对该公司起重机械安全管理不到位。
三、预防措施和整改建议
(一)起重机械使用单位应加强特种设备安全管理工作,依法履行特种设备安全主体责任,加强对起重机械作业人员的安全教育及技能培训,建立健全起重机械安全管理制度,明确岗位职责,制定科学合理的安全操作规程,督促监督作业人员按章操作,确保起重机械使用安全。
(二)充分发挥社会公众、从业人员和企业的监督作用,进一步加大对起重机械违法行为的打击力度,构建起重机械安全监管社会共治体系。
(三)进一步加大起重机械安全宣传力度,提高起重机械使用单位的安全意识和管理水平,推动企业落实安全主体责任,提高起重机械从业人员技能水平和安全防护意识。
案例9 野蛮操作 吊运管桩撞死下方员工
一、事故简介
2018年8月11日凌晨1时00分左右,某管桩公司F车间起重机操作员李某(已取得Q4有效证件)驾驶5号起重机吊运一条管桩(钢筋混凝土材质,规格:长12米,直径40厘米)从5米外的地方准备放在管桩卡位上,并在吊运过程中用起重机喇叭提醒下方人员。同在该平台拆除头板工作的张某(死者)在0时58分违反公司的安全生产规章制度,没有在工作平台指定的位置休息,而是直接坐在链条机小车的管桩卡位上休息,没有观察起重机作业情况,被李某吊运的管桩碰撞受伤身亡。
二、事故原因分析
(一)现场调查
发生事故的起重机属于双吊钩通用桥式起重机,双小车、双升降机构,在起重机2个吊钩上仍悬挂着索具,该索具为2组吊链,已停靠在一边。
通用桥式起重机规格型号为QE8+8-16.5,产品编号为Q-00787,额定起重量为16(8+8)t,起升高度为9m,起升速度为8m/min,大车运行速度为44.2 m/min,小车运行速度为45 m/min。设备注册代码为40104420002001090109,使用登记证号为“起11粤T00049(18)”。
(二)事故原因分析
1.直接原因:
(1)事故单位起重机司机李某违反《起重机械安全规程》5.1.2.2点的规定,在吊运时,明知吊臂下有人(死者张某)仍然从人的上空通过,直接导致事故发生。
(2)事故单位员工张某没有选择在工作平台上休息,直接坐在链条机的管桩卡位上休息直接导致事故的发生。
2.间接原因:事故单位员工张某安全意识淡薄,自我保护意识不强,违反公司安全生产规章制度。
三、事故警示
(一)起重机械使用单位应加强特种设备安全管理工作,依法履行特种设备安全主体责任,聘请有相应证件的人员从事起重机械作业,加强对起重机械作业人员的安全教育及技能培训工作,建立健全起重机械安全管理制度,明确各自岗位职责,制定科学合理的安全操作规程,确保起重机械安全使用。
(二)充分发挥社会公众、从业人员和企业的监督作用,进一步加大对违法行为的打击力度,构建起重机械安全监管社会共治体系。
(三)进一步加大对特种设备安全的宣传力度,提高起重机械使用单位的特种设备安全意识和管理水平,推动企业落实安全主体责任,提高群众特种设备安全使用知识和安全防范意识。
案例10 防护措施不到位 电工高空坠落致死
一、事故发生过程及伤亡情况
2018年9月21日上午,某码头公司操作部机修班电工张某、梁某两人在5号固定式起重机内进行电气线路检修作业,在检修过程中梁某移除了操作室内向下观察窗的防护铁栏,11时30分左右下班前,两人分别关闭机仓内窗户和司机室窗户。当张某关闭机仓内窗户出来时,发现梁某已坠落到司机室下方地面上,即通知公司管理人员并拨打110报警和120救护车到场。
经翻查监控视频,可清楚看到梁某由于安全意识不够,匆忙中双脚站立在司机坐椅右前方移除了防护铁栏的非承重玻璃观察窗上关闭窗户,导致玻璃破碎后直接坠落到地面上受伤,随后梁某被送往某市第一人民医院抢救,于当天16时20分抢救无效死亡。
事发设备为固定式起重机,产权单位、实际使用单位均为该码头公司,固定式起重机,型号为GQ4025,制造商:长江航务管理局武汉港机厂,出厂日期:2004年11月,出厂编号:200414,起重量(吊勾作业):40t,起升高度(码头面上/下):18m/8m,整机最大高度:34.912m,运行操作形式:室控,注册代码40304406002005010003 ,注册登记日期:2005年01月21日 ,检验有效期至2018年12月。
此次事故造成一人死亡。直接经济损失110.8万元。
二、事故原因及性质
(一)直接原因
死者梁某在5号固定式起重机维修作业时移除观察窗防护铁栏,且在作业后未盖上,由于安全意识不够,工作收尾时双脚站立在移除了防护铁栏的非承重玻璃观察窗上关闭窗户,导致玻璃破碎后从观察窗直接坠落到地面上,是事故直接原因;死者负事故主要责任。
(二)间接原因
1.因电气线路检修工作未完成,死者梁某为图省事,对底窗已没有防护栏所存在的安全隐患没有及时处理。
2.使用单位在管理上对员工安全管理、安全教育、安全措施贯彻学习力度不够;职工安全意识薄弱,自保、互保意识差。
(三)主要原因
设备维修人员安全意识差,未完全意识到高空坠落风险。
(四)次要原因
设备维修带班组长未做好设备维修安全指挥,未及时督促维修人员盖上观察窗防护栏。
经调查组讨论认为:事发时该码头公司5号固定式起重机处于停机检修状态,设备状态符合法规要求。事故是死者在电气线路检修作业过程中人为打开观察窗防护铁栏,作业后未按规定盖上观察窗防护铁栏造成人员坠落。根据《特种设备事故报告和调查处理规定》,故该事故属于特种设备事故。
三、预防措施和整改建议
(一)事故单位要立即严格开展安全隐患排查,消除人的不安全行为和物的不安全状态,提高职工安全责任心,规范职工作业行为,从根本上提高职工对安全的认识和对隐患的判断和防范能力。
(二)完善起重机械安全管理制度,严格落实执行安全管理制度及操作规程,定期组织起重机械作业人员对本岗位安全操作规程的学习,在工作中严格相关规定。
(三)事故单位要落实设备安装、维修和保养现场的施工安全,要求作业人员必须严格遵守施工现场的安全管理,依照施工方案进行施工。
(四)事故单位要立即开展安全生产教育活动,确保安全教育和培训要落到实处。
案例11 监护措施不落实 检修工被活活挤压致死
一、事故发生过程及伤亡情况
(一)事故发生过程
2018年10月12日16:35左右,某机械公司聘请的临时工闫某等3人在某钢板制品公司A区生产车间更换起重机承轨梁(以下简称“承轨梁”)紧固螺栓时,钢板制品公司员工何某在B区生产车间地面操作一台起重机(以下简称“涉事起重机”)吊运货物,何某未发现闫某的身体处于涉事起重机的大车运行区域,涉事起重机在行走过程中撞到闫某,导致闫某被涉事起重机和立柱夹住并挤压致死。事发后,钢板制品公司员工立即向110、120及119进行了报告和申请救援,消防人员到场后,将闫某救至地面,医护人员经现场抢救无效后于当天18:35左右确认闫红兵已经死亡。
涉事起重机为电动葫芦桥式起重机,注册代码为40104419001998040198,设备型号为LH10-24.35A4,额定起重量为10000kg,跨度为24.35m,控制方式为地面有线控制,单位内部编号为PG11,下次检验日期为2020年7月31日。
(二)事故伤亡情况
事故造成一人死亡,事故直接经济损失约130万元人民币。
二、事故原因及性质
(一)直接原因
闫某在钢板制品公司A区车间更换起重机承轨梁螺栓时,何某在B区车间地面操作涉事起重机吊运货物,何某未发现闫某身体处于涉事起重机的大车运行区域,涉事起重机在运行时撞到闫某,闫某被涉事起重机和立柱挤压致死。
(二)间接原因
1.机械公司未制定具体施工方案并在作业前对施工人员进行安全教育培训,事发时未对现场进行有效监护;
2.钢板制品公司未对施工现场进行有效监护及做好相应的安全防护措施。
(三)主要原因
1.机械公司施工工程安全管理不到位;
2.钢板制品公司起重机械安全管理不到位。
(四)次要原因
1.何某操作不当。
2.闫某安全防护意识不足。
三、预防措施和整改建议
(一)起重机械使用单位应加强特种设备安全管理工作,依法履行特种设备安全主体责任,加强对起重机械作业人员的安全教育及技能培训,建立健全起重机械安全管理制度,明确岗位职责,制定科学合理的安全操作规程,督促监督作业人员按章操作,同时加强对起重机械施工单位的现场安全管理监督工作,进一步提高对起重机械施工现场安全风险的防范意识,确保起重机械使用安全。
(二)起重机械施工单位应进一步加强施工现场的安全管理工作,施工前制定好相应的施工方案,做好对施工人员的安全教育及现场监督管理工作,确保起重机械施工现场的安全。
(三)进一步加大起重机械安全宣传力度,提高起重机械使用单位的安全意识和管理水平,推动企业落实安全主体责任,提高起重机械从业人员技能水平和安全防护意识。
案例12 违章操作 操作者被钢卷砸伤致死
一、事故简介
2018年10月21日某厨卫系统有限公司发生一起起重机械事故,事故造成一人死亡。
员工粟某在没有佩戴安全帽的情况下进入围栏内进行吊运作业。粟某未将回料卸出并移至备料区,便操作起重设备将新钢卷移至托盘。在未确定吊链是否完全松脱的情况下,粟某转身背向起重设备操作围栏外送料机的控制面板,期间误按起重设备遥控器向右运行按钮,使起重设备继续运行,造成托盘的倾翻,钢卷砸向粟家贵,使其受伤倒地。
事故设备情况:电动单梁起重机型号:LDA10-13.3A3D+Y,产品编号:17019002,额定起重量:10t,使用登记证编号:起17粤EC163(17),下次检验日期2019年05月,技术资料档案齐全。
二、事故原因分析
(一)事故发生的直接原因
粟某安全意识淡薄,自我防护意识较差,违反公司《吊运岗位安全环境作业指导书》(编号:JD-HSE-3-001)8.1.1“穿戴齐个人防护用品”和《吊车安全操作规程》(文件编号:QG/JD07-2-02-17.2)4.8“在吊工件时,严禁斜吊及拖拉”的规定,在没有佩戴安全帽的情况下上岗作业,在吊运作业中误操作起重设备,并有分散注意力的行为,造成起重设备斜拉钢卷,托盘倾倒,以致被运行中的钢卷砸伤。
(二)事故发生的间接原因
经过调查取证和综合分析,造成事故发生的间接原因是:
(1)事故单位制造部副部长(厂长)李某,作为公司安全生产主要负责人,督促、检查本单位的安全生产工作不到位,公司《吊车安全操作规程》和《吊运岗位安全环境作业指导书》未能及时健全,未能及时发现并消除吊运作业事故隐患。
(2)事故单位安全环保部部长彭某,作为公司专职安全生产管理人员,检查本单位的安全生产状况不到位,未能及时按照相关国家标准要求提出健全公司的《吊车安全操作规程》和《吊运岗位安全环境作业指导书》的建议。
三、事故警示
(一)事故死者粟某安全意识淡薄,自我防护意识较差,违反公司操作规程,在没有佩戴安全帽的情况下上岗作业,在吊运作业中误操作起重设备,并有分散注意力的行为,导致事故发生,对事故发生负主要责任。
(二)事故单位制造部副部长(厂长)李某,作为公司安全生产主要负责人,督促、检查本单位的安全生产工作不到位,公司《吊车安全操作规程》和《吊运岗位安全环境作业指导书》未能及时健全,未能及时发现并消除吊运作业事故隐患,违反《中华人民共和国安全生产法》相关规定,对事故发生负有责任。
(三)事故单位安全环保部部长彭某,作为公司专职安全生产管理人员,检查本单位的安全生产状况不到位,未能及时按照相关国家标准要求提出健全公司的《吊车安全操作规程》和《吊运岗位安全环境作业指导书》的建议,违反《中华人民共和国安全生产法》相关规定,彭某对事故发生负有责任。
案例十三
东莞某管桩公司“5·2”起重机械事故案例
一、事件回顾:
2016年5月2日,东莞某管桩公司起重机司机陆某(未取得起重机械司机证件)利用起重机将3根管桩吊运至货车上,在卸货完成后,陆某违规操作,在未能确定自制吊具完全起升到管桩最高处以上时,运行大车运行机构,引起自制吊具意外钩起1根管桩,产生斜拉后自制吊具从管桩内孔脱落,导致该管桩坠落,砸中从货车旁边经过的朱某,致其死亡。
二、事故原因:
1.直接原因:陆某违规操作导致管桩坠落,砸中朱某,致其死亡。
2.间接原因:
(1)东莞某管桩公司起重机械安全管理不到位;
(2)陆某无证操作;
(3)朱某违规进入作业区域。
3.事故的主要原因:
(1)陆某违规操作,无证操作;
(2)东莞某管桩公司起重机械安全管理不到位。
4.事故的次要原因为:朱某违规进入作业区域。
案例十四
深圳某港口机械公司“2·24”起重机械事故案例
一、事件回顾
2016年2月24日,深圳市南山区招商街道蛇口集装箱码头发生一起起重机械挤压事故,造成一人受伤经抢救无效死亡,直接经济损失146万元。详细经过如下:
2016年2月24日下午13时30分左右,深圳某港口机械公司驻蛇口码头桥吊组组长何某(事故受害人)接到蛇口码头公司工程部岸桥组对QC47#岸桥(事故设备)起升钢丝绳润滑的工作任务,随即安排该公司员工蔡某与其本人共同执行,何某是该工作任务的项目负责人兼指挥手,蔡某负责执行具体润滑任务,蛇口码头公司安排其作业人员黄某协助配合。起升钢丝绳润滑作业依次分为机房卷筒、后大梁平台处、主梁与前大梁铰点附近、前大梁端部四个位置。当日15时30分左右,在完成铰点附近钢丝绳润滑工作后,何某、蔡某在小车顶收拾好工具物料,随后何某用对讲机指挥黄某将吊具拉到最高处后将小车从第三工位慢速向前移动至第四工位前大梁端部位置,此时蔡某蹲在小车顶右前区域,朝向前方靠海一侧,何某在蔡某左后边即小车顶左后区域,然后小车开始启动慢速往前移动。在小车还有几米到达大梁最前端时,蔡某听到何某“哎哟”声就立即用对讲机呼叫“停车”,小车马上停下,蔡某回头看到何某被夹在前大梁左侧减速传感器支架和小车左后侧液压缓冲器无杆腔及支座之间,当时何某意识清醒,叫蔡某和黄某帮助他侧身并扶起至小车顶中间位置,随即黄某通知岸桥组主任张某赶到现场,发现何某受伤情况后,紧急拨打120急救电话,大约16:00左右,120急救车到达现场,约16:30左右,120急救车将伤者送到蛇口人民医院,经医院抢救无效死亡。
二、事故原因
(一)直接原因
事故发生后,南山市场监督管理局委托深圳市特种设备安全检验研究院对事发起重机进行了技术勘验。根据该院出具的编号为2016AHJ40009的《特种设备事故技术分析报告》显示,事发起重机质量、安全性能满足相关要求,此次事故与设备相关结构及机构的安全性能无直接关联,这次事故的直接原因是起重机维保工(何某)违反操作规程,在岸桥小车开动过程中,没有退回司机室顶部安全位置,而是进入小车架顶部的作业禁入区域,以致被岸桥小车挤压导致其受伤死亡。
(二)间接原因
深圳某港口机械公司在日常生产安全管理制度落实上存在问题:
1、未履行应有的责任义务,对员工进行足够的技能和安全培训,作业维保人员的安全意识淡薄;
2、安全制度落实不到位,对日常起重机维保现场的巡查管控措施不力,对发现的违规作业现象未能及时制止;
3、事故现场维保作业人员何某不严格依规按章维保起重机械设备,个人作业行为随意,其应急反应和处置能力明显不足。
中山“2·23”起重机械坠落事故案例
一、事件回顾
2016年2月23日,中山市某管桩公司第三堆放场发生1起起重机械使用过程由于卸吊的管桩坠落致1人死亡的特种设备事故。事故详细经过如下:
2016年2月23日晚上21:12左右,中山市某物流公司平板运输车司机刘某驾驶平板运输车(车头号牌为粤T14510、拖挂车号牌为粤T0974挂)从中山某管桩公司M堆场转运“φ500m X 13m”管桩到DE3#堆场,因当班持证的起重机司机请假,堆场的司索工(挂钩手)郭某便擅自操作起重机进行管桩吊卸,并由平板运输车司机刘某配合进行管桩司索作业(挂钩)。当吊卸到倒数第二层的最靠边那根管桩时,刘某先挂好了靠近驾驶室那一端的索具,再到另一端进行挂钩。站在车上进行挂钩作业的刘某挂钩完毕跳下车厢尚未走到安全区域,郭某便操作起重机起吊管桩。在起吊过程,靠近车尾一端的索具突然脱钩,刘某趴在地上躲过了坠落的管桩,但紧接着管桩另一端的索具也脱钩,整根管桩坠落到地面后往回(靠近平板运输车方向)滚动,刘某躲避不及被往回滚动的管桩碾压到头部,抢救无效死亡。
二、事故原因
(一)事故的直接原因:
1.中山某物流公司司机车刘某,违规擅自进行管桩挂钩作业,因未经过司索作业(挂钩)岗前培训,未掌握挂构操作要领,操作不当(挂钩未到位);
2.中山某管桩公司员工郭某(普工)无证上岗,擅自操作起重机进行管桩装卸作业,在操作中未能及时发现挂钩未到位的不正常状态且未等刘某走到安全区城便开始起吊管桩,导致在起吊过程索具脱构、管柱坠落酿成事故。
(二)事故的间接原因:
中山某物流公司刘某安全意识淡薄,自我保护意识不强,在起重机升降过程未按规定站在安全区域,管桩坠落时躲避不及被碾压致死。
(三)事故的主要原因:
1.中山某管桩公司员工郑某(班长)在明知郭某未取得相应的特种设备作业人员证的情况下,仍安排其在起重机持证司机不足时顶替起重机司机操作起重机进行管桩装卸作业;
2.中山某管桩公司员工郭某未经培训、考核,未取得相应的特种设备作业人员证,违章操作起重机导致事故发生。
(四)事故的次要原因:
1.中山某管桩公司场地主管蒋某、安全办主任刘某、生产部经理刘胜某、总经理赖某等各级安全管理人员、相关责任人安全意识和责任心不强,制度执行不严,监督检查不力;
2.中山某管桩公司对新员工以及外协单位员工的安全培训、安全教育和管理不到位;
3、中山某物流公司对司机的安全管理制度不完善。